李滄專業(yè)工裝生產(chǎn)商
發(fā)布時間:2022-01-09 01:22:31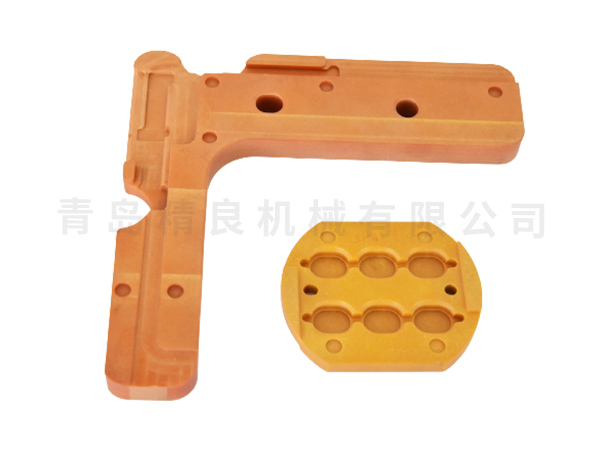
李滄專業(yè)工裝生產(chǎn)商
大家都知道,機械設(shè)備零部件加工失效的緣故有很多。但是,大家怎么才能知道機械設(shè)備零部件加工失效的緣故呢?下邊就和機械設(shè)備零部件加工生產(chǎn)加工一起來研究一下吧。1.當(dāng)場觀查科學(xué)研究,這短長常焦慮不安的一步,盡量細心搜集失效零部件的遺骸,并拍照記錄時況,從而搞清楚關(guān)鍵分析的專用工具,樣品應(yīng)源自失效的來源于影響力。2.細心記錄并整理失效零部件的有關(guān)材料,如方案圖.生產(chǎn)制造方法及應(yīng)用情況。3.對所選定的試樣舉辦分析,搞清楚失效的起源點和失效的方法。透射電鏡斷裂面分析明確失效起源地和失效方法;金相分析分析,明確材料的里邊質(zhì)量。

李滄專業(yè)工裝生產(chǎn)商
1.機械零件常用材料: -般碳素結(jié)構(gòu)鋼( Q屈從強度)高質(zhì)量碳素結(jié)構(gòu)鋼( 20均勻碳的質(zhì)量分?jǐn)?shù)為萬分之20 )、合金結(jié)構(gòu)鋼 ( 20Mn2錳的均勻質(zhì)量分?jǐn)?shù)約為2% )、鑄鋼 ( ZG230-450屈從點不于230 ,抗拉強度不小于450 )、鑄鐵 ( HT200灰鑄鐵抗拉強度)2.常用的熱處理方法:退火(隨爐緩冷)、耿(在空氣中冷卻)、淬火(在水或油中敏捷冷卻)、回火(吧淬火后的零件再次加熱到低于臨界溫度的固定溫度,保溫一-段時間后在空氣中冷卻)、調(diào)質(zhì)(淬火+高溫回火的進程)、化學(xué)熱處理(滲碳、滲氮、碳氮共滲)3.機械零件的結(jié)構(gòu)工藝性:便于零件毛坯的制造、便于零件的機械加工、便于零件的裝卸和可靠定位。

李滄專業(yè)工裝生產(chǎn)商
(2)調(diào)整法:預(yù)先用樣件或規(guī)范件調(diào)整好機床、夾具刀具和工件的確定相對方位,用以確保工件的尺度精度。因為尺度事前調(diào)整到位,所以加工時,不必再試切,尺度自動取得,并在一批零件加工過程中堅持不變,這便是調(diào)整法。例如,選用銑床夾具時,刀具的方位靠對刀塊確認(rèn)。調(diào)整法的本質(zhì)是使用機床上的定程設(shè)備或?qū)Φ对O(shè)備或預(yù)先整好的刀架,使刀具相對于機床或夾具到達固定的方位精度,然后加工一批工件。在機床上依照刻度盤進刀然后切削,也是調(diào)整法的一種。這種辦法需求先按試切法決議刻度盤上的刻度。大批量出產(chǎn)中,多用定程擋塊、樣件、樣板等對刀設(shè)備進行調(diào)整。調(diào)整法比試切法的加工精度安穩(wěn)性好,有較高的出產(chǎn)率,對機床操作I的要求不高,但對機床調(diào)整I的要求高,常用于成批出產(chǎn)和大量出產(chǎn)。
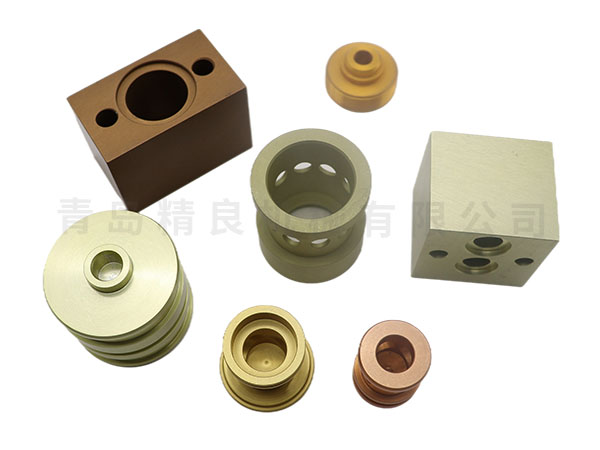
李滄專業(yè)工裝生產(chǎn)商
加工精度是指零件加工后的實踐幾許參數(shù)(尺度、形狀和方位)與圖紙規(guī)定的抱負(fù)幾許參數(shù)契合的程度。這種相契合的程度越高,加工精度也越高。在加工中,由于各種因素的影響,實踐上不可能將零件的每一個幾許參數(shù)加工得 與抱負(fù)幾許參數(shù)完全相符,總會發(fā)生一些違背。 這種違背,便是加工誤差。一、取得零件尺度精度的辦法:(1)試切法:即先試切出很小部分加工表面,丈量試切所得的尺度,依照加工要求恰當(dāng)調(diào)刀具切削刃相對工件的方位,再試切,再丈量,如此通過兩三次試切和丈量,當(dāng)被加工尺度到達要求后,再切削整個待加工表面。試切法通過‘”試切-丈量-調(diào)整 再試切”, 反復(fù)進行直到到達要求的尺度精度停止。例如,箱體孔系的試鏜加工。
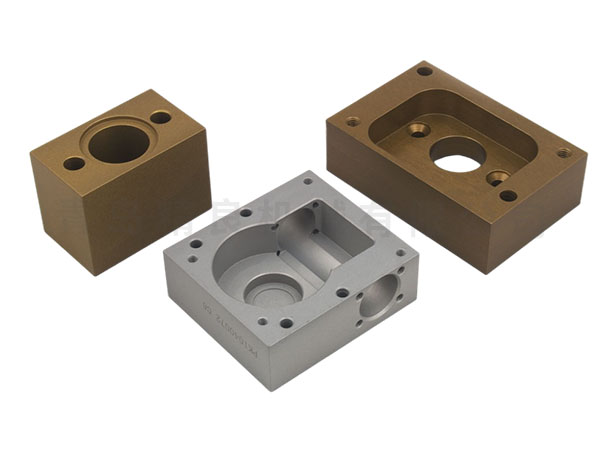
李滄專業(yè)工裝生產(chǎn)商
為了提高機械零件加工質(zhì)量,需要找出造成加工誤差的主要因素,這是關(guān)鍵,需要采取相應(yīng)的措施來減少或控制這些因素的發(fā)生。一、誤差分組法:該方法根據(jù)誤差大小將精加工或在線加工的工作尺寸分成n組,然后根據(jù)誤差范圍調(diào)整刀具相對于工件的位置。二、誤差補償法:這種方法的主要目的是創(chuàng)建新的原始誤差,抵消原始工藝系統(tǒng)固有的原始誤差,從而達到降低加工誤差和加工精度的目。三、誤差轉(zhuǎn)移法:該方法實質(zhì)上是將工藝系統(tǒng)的幾何誤差、 受力變形和熱變形等轉(zhuǎn)移到不影響加工精度的方向。例如,對于具有分級或轉(zhuǎn)級的多工位工序或采用轉(zhuǎn)級刀架加工的工序,其分級、轉(zhuǎn)級企業(yè)家誤差直接影響零件表面的加工精度。